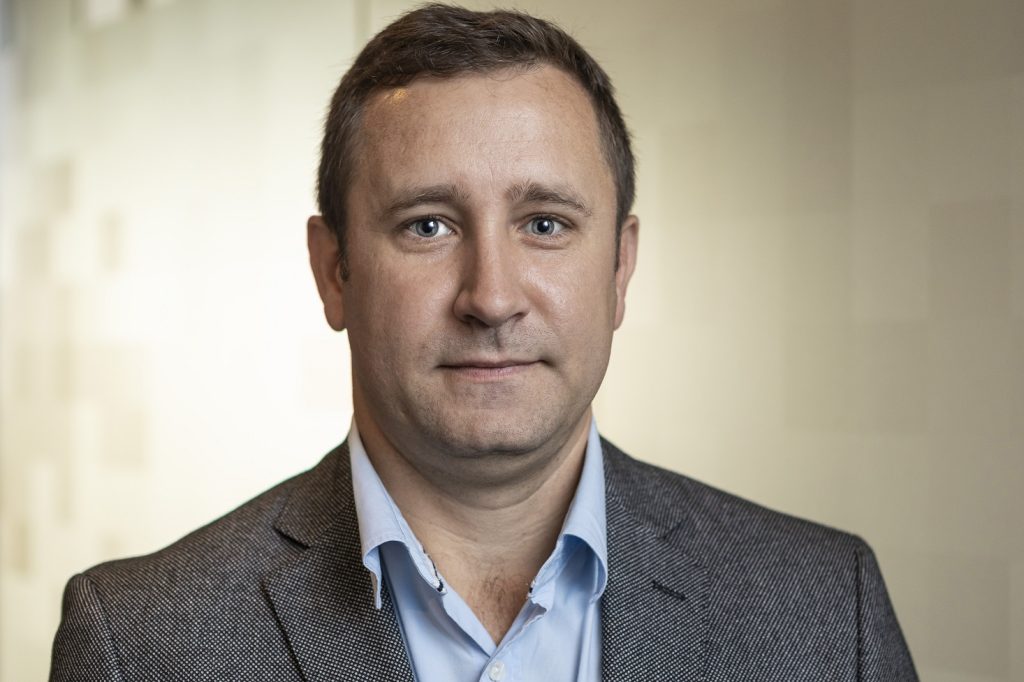
Marius Wessels
The manufacturing industry is constantly evolving, driven by rapid technological advancements, shifting market demands, and global trends. While much of the spotlight is on artificial intelligence (AI), other innovative technologies like digital twins are playing a crucial role in revolutionising the manufacturing sector. Digital twin technology, which creates virtual replicas of physical systems, enables manufacturers to optimise processes, predict maintenance needs, and enhance overall efficiency. This transformative approach is not only fostering digital transformation but also paving the way for smarter, more agile manufacturing operations.
What is Digital Twin Technology?
Digital twin technology involves creating a virtual replica of a physical object, person, or process, allowing for the simulation of its behaviour to better understand real-world operations. By simulating real situations and their outcomes, digital twins enable organisations to make more informed decisions.
When digital twins are linked to real-time data sources from the environment, they continuously update to reflect their physical counterparts. This real-time mirroring includes behavioural insights and visualisations derived from data. When interconnected within a unified system, digital twins form what’s known as an enterprise metaverse – a digital, often immersive environment that replicates and connects every aspect of a company. This comprehensive replication enhances simulations, scenario planning, and decision-making, ultimately optimising operations.
The potential of digital twins to deliver more agile and resilient operations is increasingly recognised by industry leaders. McKinsey research indicates that 70% of C-suite technology executives at large enterprises are already exploring and investing in digital twin technology.
There are several types of digital twins, each serving different purposes. For manufacturers, the product twin is particularly relevant. A product twin represents a product throughout various stages of its lifecycle, from initial concept design and engineering to full functionality. This means manufacturers can access live, real-time data on a product as if it were in service.
A prime example of a product twin in action is seen in the automotive industry with Volvo. Renowned for prioritising passenger safety, Volvo uses digital twins to create virtual replicas, allowing them to test and refine different materials and aerodynamics in new vehicle designs.
Product digital twins are also invaluable in improving sustainability efforts. They help manufacturers reduce material usage in product design and enhance traceability, thus minimising environmental waste. Consumer electronics manufacturers, for instance, have achieved significant sustainability improvements by employing digital twins, reducing scrap waste by approximately 20%.
The Advantages for a Manufacturing Environment
Digital twin technology offers significant advantages for manufacturers, particularly in reducing time to market. By allowing rapid iterations and optimisations of product designs, digital twins enable manufacturers to test virtually, eliminating the need to physically test every single prototype. This not only speeds up the development process but also leads to substantial improvements in product quality. By simulating the product throughout the manufacturing process, potential flaws can be identified and addressed much earlier.
Digital twins streamline product development through virtual testing and manage the entire lifecycle of assets – from design and production to operation and maintenance. Product development leaders anticipate that digital twins will accelerate development processes, enhance outcomes, and reduce costs. The enthusiasm for this technology is evident, with the global market for digital twin technologies projected to grow at an annual rate of about 60% over the next five years.
Beyond product development, digital twins help the manufacturing industry work faster and smarter by improving factory floor configurations, reducing downtime, and providing deeper insights into physical assets. They can also model the entire supply chain, from raw materials to finished products, optimising logistics, inventory management, and distribution.
Implementing digital twin technology doesn’t have to be an all-or-nothing approach. Companies can begin their journey towards an enterprise metaverse with a single digital twin, modelled after one data product. A data product is a high-quality, ready-to-use dataset that can be easily accessed and applied across an organisation. It serves as a single, reusable source of truth that can be enhanced over time, forming the basis for future use cases. As the initial digital twin evolves based on behavioural data insights, it provides increasingly powerful predictive capabilities.
From this starting point, manufacturers can create multiple interconnected digital twins to simulate complex relationships between different entities. This interconnected network generates richer behavioural insights, enabling more sophisticated use cases and delivering greater value.
Digital Maturity is a Critical Component
For manufacturers aiming to implement digital twins, digital maturity is essential. This maturity hinges on having a robust data infrastructure that delivers reliable data from both testing and live environments, coupled with the talent needed to build and maintain that infrastructure.
However, manufacturers don’t necessarily need a complex or dynamic environment to benefit from digital twins. Success can be found in twinning even simple products, like toothbrushes, to gain real-time customer feedback. Once the initial use case is established, companies can add more layers of information and real-time feedback, continually enhancing the twin.
While digital twin technology may seem like a futuristic concept to many African manufacturers who are just beginning their digital transformation journey, it is already reshaping smart manufacturing. By embracing digital twins, manufacturers can drive innovation, improve efficiency, and secure a competitive edge in an increasingly complex and dynamic market.
Marius Wessels, Manager: Professional Services for SYSPRO Africa. He writes in his personal capacity.
INFO SUPPLIED.